
Although electrodeposited copper has greater tensile strength and elongation before breaking, rolled copper has better elastic elongation before reaching permanent deformation.

Under similar conditions, rolled copper has significantly improved resistance to cracking.
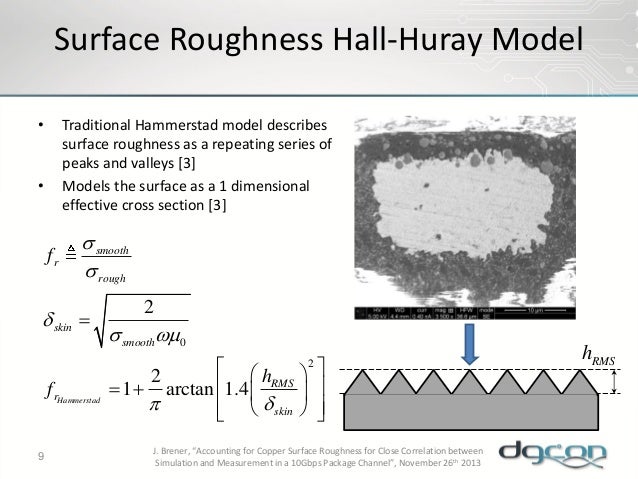
Hammerstad and Jensen, incorporated Morgan’s model, along with correlated data in microstrip design method. Morgan published results of numeric simulations that indicated that a factor of two increase in conductor loss could be caused by surface roughness. It has been well-known since the earliest days of microwave engineering with wave guides that the conductor surface roughness can substantially affect the conductor loss. Of course, the rolled copper with no surface treatment is typically the smoothest. The surface roughness of different copper weights (oz) is different. Roughness data of electrodeposited (ED) and rolled (RA) copper foils with different thicknesses was obtained by using an optical surface profile. However, in our experience, the Sq (RMS) profile as measured by white light interferometry of the treated side of copper foil correlates between conductor losses. Many sources report the Rz (peak to valley) profile as measured by a mechanical profilometer. Surface roughness can be measured by mechanic and optical methods. This is surface roughness, and which has effects on the performance of high-speed PCBs. To the naked eye, coppers appear smooth, but at the microscopic level, copper foils and copper on laminates exhibit surface irregularities.
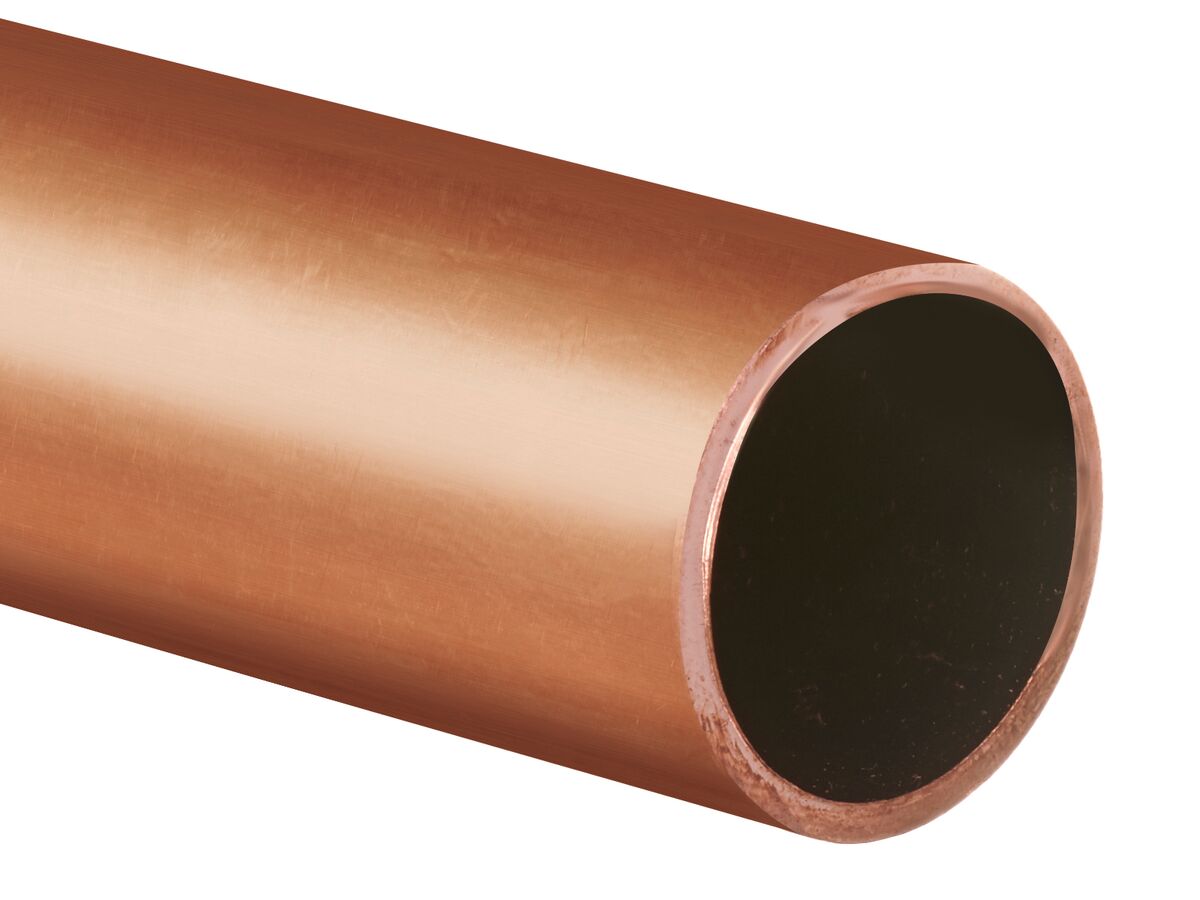
What’s copper surface roughness? As a PCB design and manufacturing company, MADPCB understands it well. In high-speed design (HSD) and fabrication, we always meet the roughness of the conductor’ surface, which is called conductor or copper surface roughness.
